1.焊前准备
1. Preparation before welding
(1)根据板厚形式,采用机械加工、等离子孤切割或碳弧气刨等方法下料加工坡口,为了避免飞溅金属损伤,在使用碳弧气刨和开坡口和手工电弧焊接时,应在坡口两侧涂上石灰粉。
(1) According to the form of plate thickness, the groove shall be cut by machining, plasma arc cutting or carbon arc gouging. In order to avoid splashing metal damage, lime powder shall be coated on both sides of the groove when carbon arc gouging, beveling and manual arc welding are used.
(2)坡口形式宜采用V 形坡口,要采用较小的焊接电流,这样可以防止不锈钢产生晶间腐蚀。
(2) V-shaped groove shall be adopted for groove form, and small welding current shall be adopted, so as to prevent intergranular corrosion of stainless steel.
(3)为了满足接头具有相同的性能,应遵循“等成分”原则来选择焊接材料,同时要注意接头中的铁素体不能太多,这样是为了增强接头抗热裂纹和晶间腐蚀能力。
(3) In order to meet the same performance of the joint, the welding material shall be selected according to the principle of "equal composition". At the same time, it shall be noted that there shall not be too much ferrite in the joint, so as to enhance the heat crack and intergranular corrosion resistance of the joint.
(4)应采用严格的定位焊,遵循“短而厚”、“点焊不焊透”的原则。
(4) Strict tack welding shall be adopted and the principles of "short and thick" and "spot welding without penetration" shall be followed.
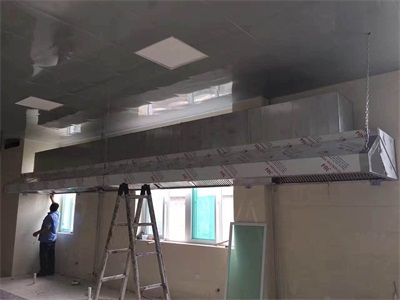
2.焊接技术要求
2. Welding technical requirements
(1)手工电弧焊时焊机应采用直流反接,氩弧焊时应采用直流正接。
(1) DC reverse connection shall be adopted for manual arc welding and DC positive connection shall be adopted for argon arc welding.
(2)在焊接前,应将焊丝用不锈钢丝刷掉表面的氧化皮,并用丙酮清洗,然后进行烘干,随取随用。
(2) Before welding, the welding wire shall be brushed off the oxide scale on the surface with stainless steel wire, cleaned with acetone, and then dried for use at any time.
(3)打底焊时焊缝厚度应尽量薄,这样利于与根部熔合良好;收弧时要成缓坡形,如有收弧缩孔,应用磨光机磨掉。要在坡口内引弧熄弧,熄弧时应填满弧坑,防止弧坑裂纹。
(3) During backing welding, the weld thickness shall be as thin as possible, which is conducive to good fusion with the root; The arc closing shall be in a gentle slope shape. If there is arc closing shrinkage, it shall be ground off with a grinder. Arc striking and extinguishing shall be carried out in the groove. During arc extinguishing, the arc pit shall be filled to prevent arc pit cracks.
(4)为了防止碳化物析出敏化及晶间腐蚀,应严格控制层间温度和焊后冷却速度,所以要求焊接时层间温度控制在60℃ 以下。
(4) In order to prevent carbide precipitation sensitization and intergranular corrosion, the interlayer temperature and cooling rate after welding should be strictly controlled, so the interlayer temperature during welding is required to be controlled below 60 ℃.
(5)在施焊时尽量使用氩弧焊摇把技术,该技术能很好的控制焊层表面颜色以及成形,焊接效果比较理想。
(5) Argon arc welding crank technology shall be used as much as possible during welding. This technology can well control the surface color and shape of welding layer, and the welding effect is ideal.
上一篇:安装工人需要知道哪些通风管道知识?
下一篇:山东通风管道加工哪家好?